Here are the reasons why companies like HP, Philips, Cummins, Schumacher Electric, Johnson Controls, BorgWarner, and Motorola choose AMREP for quality engineering needs:
TRUST
Professional integrity, reliability, independence, and honesty.
PROFESSIONAL EXPERTISE
Solid records of achieving positive production outcomes and strong technical acumen.
CUSTOMER CARE
Individual client care with 24/7 service. Professionally crafted solutions that perfectly meet the client's needs.
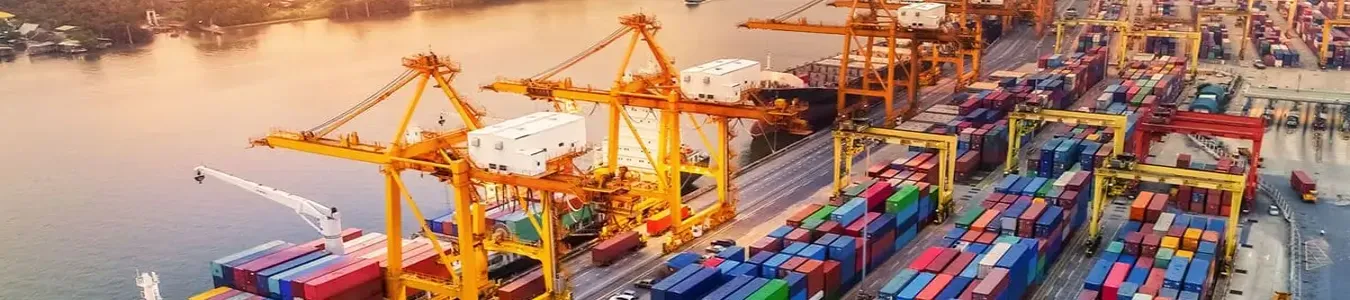
Solve one of the biggest challenges in manufacturing - how to sustain and improve quality performance at your production site - with AMREP's quality engineering team! If you're concerned about quality 'slippages' at your production or supplier site, if you worry that your requested follow-up actions are not being executed, then we are the answer.
We work at your production facility to maintain quality performance, drive supplier actions, and resolve production problems before they escalate through your production line and supply chain. Our actions can range from small remedial actions to expansive sustaining quality engineering programmes.
- Supplier quality process monitoring
- Corrective actions closures
- Supplier follow-ups and action closure
- Production and quality line auditing
- Process controls
- Problem resolution
- Sustaining quality engineering activities
- Program management
- Material and design reviews
- QMS implementation
- NPI development
- Initial Production Set-Up/NPI
- Data collection
- Process improvement
- Supplier training, coaching, and technical skills augmentation
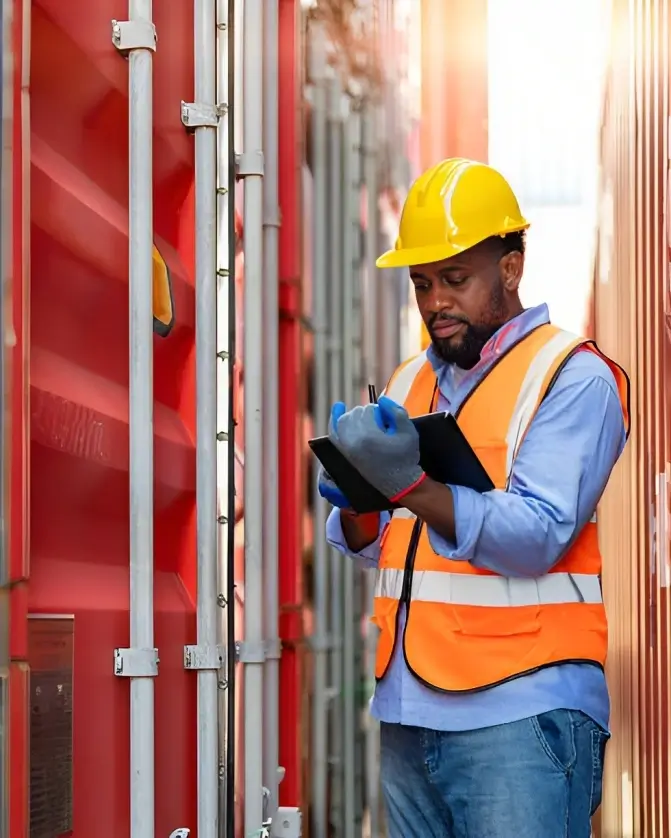
John D.,
Quality Manager"AMREP's Quality Enhancement Services have been a game-changer for our production processes. Their expertise in implementing ISO 9001 compliant quality management systems has significantly reduced our defect rates and improved overall efficiency. I highly recommend their services to any manufacturing business looking to enhance their quality standards.”
Sarah K.,
Operations Director"Working with AMREP has been a seamless experience. Their team of quality engineers brought a wealth of knowledge and innovative solutions to our company. We saw immediate improvements in our quality control processes, which led to higher customer satisfaction and fewer production delays. AMREP's commitment to excellence is truly commendable."
Michael L.,
Senior Engineer"AMREP provided us with tailored quality engineering solutions that perfectly addressed our specific needs. Their thorough inspections and process improvements have been instrumental in ensuring our products meet the highest standards of quality. Their proactive approach and continuous support have made a significant impact on our operations."
Emily R.,
Quality Assurance Lead"The training and development programs offered by AMREP were exactly what our team needed. Their workshops on Lean and Six Sigma methodologies have empowered our staff to drive continuous improvement initiatives within our organization. AMREP's dedication to quality and their customer-centric approach make them a trusted partner."
James P.,
Plant Manager"AMREP's comprehensive supplier quality management services have streamlined our supply chain and improved the reliability of our products. Their detailed audits and ongoing collaboration with our suppliers have resolved long-standing quality issues and enhanced our overall production process. We are extremely satisfied with the results."
Olivia H.,
Quality Control Supervisor"The expertise and professionalism of AMREP's team have exceeded our expectations. Their advanced inspection techniques and root cause analysis have helped us identify and rectify issues promptly. Their support has been invaluable in maintaining our ISO 9001 certification and driving continuous improvement."
Ready to elevate your manufacturing quality standards? Contact AMREP today to learn more about our tailored Quality Assurance Services and discover how we can help you achieve excellence in your production processes. Don't wait – ensure top-notch performance and compliance with AMREP by your side. Reach out now for a consultation!
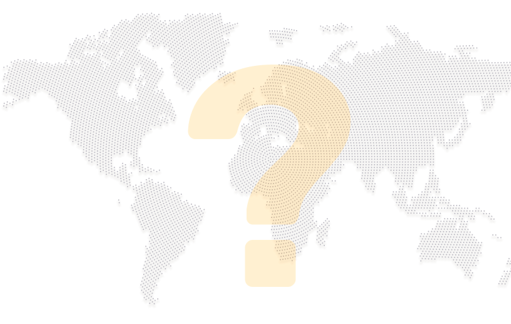
MQE focuses on improving the quality and efficiency of manufacturing processes. It involves implementing quality management systems, conducting inspections, and employing continuous improvement techniques to ensure products meet or exceed quality standards.
We serve a wide range of industries, including automotive, aerospace, electronics, medical devices, consumer goods, and more. Our solutions are tailored to meet the specific quality challenges of each industry.
We employ various methodologies such as Lean, Six Sigma, and Total Quality Management (TQM). These approaches help identify inefficiencies, reduce waste, and enhance productivity within your manufacturing processes.
We use a combination of advanced inspection techniques, root cause analysis, and continuous monitoring to ensure the effectiveness of our solutions. Our team conducts regular audits and assessments to verify that improvements are sustained over time.
Yes, we offer comprehensive supplier quality management services. This includes evaluating and qualifying suppliers, conducting regular performance audits, and collaborating with suppliers to resolve quality issues and drive improvements.
Absolutely. We offer customized training programs on quality management principles and practices. Our workshops and seminars cover various topics, including Lean, Six Sigma, and other quality improvement methodologies.
We provide in-depth inspection and testing services for raw materials, in-process components, and finished products. Our services include non-destructive testing (NDT), coordinate measuring machines (CMM) inspections, and more, ensuring comprehensive quality assurance.
We conduct thorough root cause analysis (RCA) to identify the source of quality issues. Based on our findings, we develop and implement corrective and preventive actions (CAPA). We also follow up to ensure these actions are effective and prevent recurrence.
AMREP services are distinguished by extensive industry expertise, customized solutions, use of advanced technology, and proactive quality management approach. We focus on delivering tangible improvements and long-term results for our clients.
Getting started is easy. Contact us to schedule an initial consultation. We will discuss your specific needs, assess your current quality management processes, and develop a tailored plan to help you achieve your quality goals.
A manufacturing quality engineer is a professional responsible for ensuring that manufacturing processes and products meet established quality standards. Their roles and responsibilities include:
-
Developing and implementing quality management systems (QMS).
-
Conducting inspections and audits to ensure compliance with quality standards.
-
Analyzing production processes to identify areas for improvement.
-
Collaborating with cross-functional teams to resolve quality issues.
-
Implementing corrective and preventive actions (CAPA) to address quality problems.
-
Training staff on quality management practices and procedures.
-
Maintaining documentation and records related to quality control and assurance.
Quality engineering in manufacturing is crucial for ensuring that products meet customer expectations and comply with industry standards. It helps in reducing defects, minimizing waste, and improving overall efficiency. Common methodologies used in quality engineering include:
-
Lean Manufacturing: Focuses on eliminating waste and optimizing processes.
-
Six Sigma: Uses statistical tools to identify and reduce variability in processes.
-
Total Quality Management (TQM): A comprehensive approach that involves all employees in continuous quality improvement.
-
Statistical Process Control (SPC): Monitors and controls processes through statistical methods to ensure consistent quality.
-
Failure Mode and Effects Analysis (FMEA): Identifies potential failure points and their impacts to prevent issues before they occur.
Reach out today to discuss how our quality enhancement services can elevate your production standards. Our experts are ready to tailor solutions that meet your specific needs.
Call Us
(00) 112 365 489
Mon - Sat 9.00 - 18.00
Sunday Closed
