Vietnam's market is thriving, with strong economic growth averaging 6-7% per year over the past decade. The population is mostly young and tech-savvy, with over 60% under 35 years old, leading to a growing middle class expected to reach 33 million by 2025. As a major global manufacturing hub, Vietnam’s exports reached around $350 billion in 2022, particularly in textiles, electronics, and consumer goods. To succeed in this dynamic market, it’s important to understand local regulations, quality standards, and cultural differences, making effective quality control and inspection services essential for achieving success.
Ensuring Your Products Meet the Highest Standards
Pre-Production Inspection (PPI)
Set the Stage for Success
Before production begins, our Pre-Production Inspection helps verify materials and production plans to ensure alignment with your specifications. By addressing potential issues upfront, we help you avoid costly mistakes down the line.
- Material Verification: Material Verification:
- Supplier Capability Assessment: Evaluate supplier readiness and reliability.
- Production Process Review: Ensure processes are in place to meet quality expectations.
During Production Inspection (DPI)
Stay Ahead of Quality Control
Our During Production Inspection provides ongoing checks throughout the manufacturing process. This proactive approach ensures that any defects are caught early, minimizing waste and delays.
- In-Line Inspections: Conduct checks at various production stages.
- Workmanship Verification: Ensure adherence to quality standards.
- Real-Time Reporting: Receive updates on production progress and quality levels.
Pre-Shipment Inspection (PSI)
Final Check Before Dispatch
Our Pre-Shipment Inspection is your last line of defense against quality issues. We thoroughly inspect products before they leave the factory, ensuring they meet your specifications and contractual obligations.
- Comprehensive Inspections: Assess quality, quantity, and packaging.
- Detailed Reporting: Receive a full report and certification of compliance.
- Risk Mitigation: Prevent costly returns and enhance customer satisfaction.
Container Loading Supervision
Secure Your Products in Transit
Our Container Loading Supervision service ensures that products are loaded safely and securely, minimizing the risk of damage during transportation.
- Loading Process Monitoring: Supervise the loading to ensure proper techniques.
- Container Integrity Verification: Check for any potential issues with containers.
- Documentation: Maintain records of loading conditions for your peace of mind.
Factory Audits
Ensure Compliance and Quality
Our Factory Audit service evaluates manufacturing facilities for compliance with quality standards and ethical practices. We provide insights that can help improve processes and enhance overall quality.
- Comprehensive Audits: Evaluate processes, management systems, and working conditions.
- Actionable Recommendations: Receive a detailed report with improvement suggestions.
- Global Compliance: Align with international quality and safety standards.
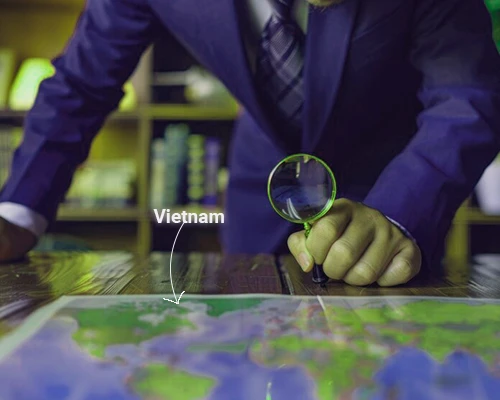
We provide our quality inspection services throughout Vietnam, including major manufacturing hubs such as:
- Ho Chi Minh City
- Hanoi
- Da Nang
- Binh Duong
- Hai Phong
Hear what our clients have to say about their experiences with AMREP's quality inspection services
Kathleen Morgan, Engineering Director
Electronics/ consumer techOur company makes cutting edge robotic solutions for aged care. We’re a small company who needed to focus our resources on developing our engineering team; it would have been really expensive for us to develop our own in-house quality and manufacturing team. We found that AMREP was an excellent way of outsourcing our QA/QC function at an affordable cost - we obtained the expertise we needed, and we had AMREP engineers who could work directly with our vendors to implement our manufacturing requirements.
Hayley Williams, Director of Manufacturing
Consumer ProductsAMREP is our pre-shipment inspections partner at our sourcing locations in Asia and Mexico. We’ve been with them for more than 10 years. We like that their quality engineers and operations managers train the inspector teams themselves and take the time to properly study our products so that they apply the right inspection techniques.
Charles Bateman, Director of Operations
Health TechChoosing AMREP’s supplier management solutions was a brilliant move for our business. By having an AMREP SQE at our contract manufacturer site in Mexico, we saved considerable amounts of time and money in having to send our own team over although we’re based in the US. One major advantage was having somebody onsite who could follow up on the CAPA items we requested of the supplier.
Henry Jackson Lee, Director of Supply Chain
Medical devicesWe use AMREP Supplier Management Services to do source inspections and sustaining quality engineering activities at our final assembly site in China. Being in the medical devices industries, we are naturally extremely concerned about quality escapes in our supply chain. AMREP’s inspectors and quality engineers helped us to foster a quality management discipline at our supplier and reduce production issues.
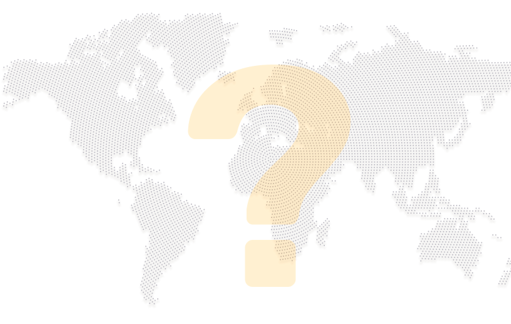
We provide quality inspection services across a diverse array of industries. Our primary sectors include textiles, electronics, furniture, consumer goods, automotive parts, and food products.
Our inspectors are our greatest asset, and we invest significantly in their training and development. Each inspector undergoes a rigorous selection process, followed by extensive training on international quality standards, inspection techniques, and industry-specific guidelines. They are also required to obtain relevant certifications and attend regular workshops to stay current with evolving standards and practices. This continuous education ensures that our inspectors are equipped with the latest knowledge and skills to deliver accurate and reliable inspection services.
Absolutely! We understand that the manufacturing environment can be unpredictable, and urgent needs may arise. Our flexible scheduling allows us to accommodate inspections on short notice whenever possible. Once you reach out to us, we will work quickly to arrange an inspection that fits your timeline, ensuring minimal disruption to your production process.
We prioritize timely communication and reporting. Typically, you can expect to receive your inspection report within 24 hours of the completion of the inspection. Our reports are detailed and comprehensive, providing insights into the inspection findings, along with photographs and recommendations. In some cases, particularly for more complex inspections, the turnaround time may vary slightly, but we always keep our clients informed throughout the process.
Getting started with our quality inspection services is simple! You can contact us via our website's contact form or by phone. One of our knowledgeable representatives will be happy to assist you. We’ll discuss your specific needs, explain our services in detail, and guide you through the process. From there, we can schedule an inspection that best suits your requirements and timeline. We are here to ensure your experience is smooth and efficient!
Reach out now and one of our knowledgeable representatives will guide you through our services and how they can be tailored to meet your business objectives.
Leverage agile framewokrs to provide a robust synopsis for strategy collaborative thinking to further the overall value proposition.
Call Us
(00) 112 365 489
Mon - Sat 9.00 - 18.00
Sunday Closed
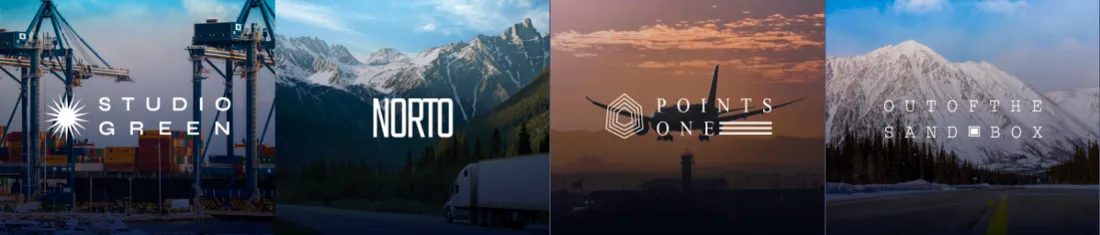
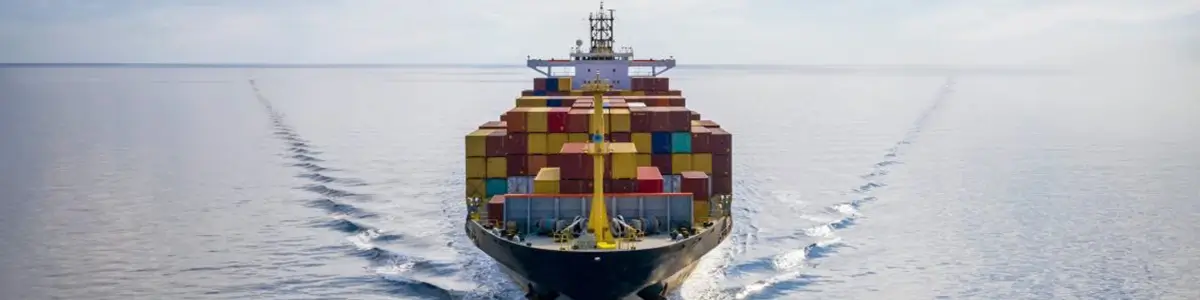