Our quality solutions range from once-off pre-shipment inspections to comprehensive production/supplier quality management programs. We don't just find quality defects. We work on-site with your suppliers to maintain product conformity, consistent quality performance, and alignment with your quality and production requirements.
Supplier Audits
Assessing your site's production readiness, QMS, standards compliance, and production processes.
Source Inspections
Source inspections, pre-shipment inspections, process inspections, first article inspections, final inspections. Capturing quality issues and defects, from the individual component level to the final product.
Supplier Quality Engineering
Implementing in-production quality process controls and driving quality improvements. Problem-solving, follow-ups, process monitoring, corrective actions, supplier quality engineering.
Supplier Development
Supplier development and production improvement programs to generate cost savings and efficiency gains.
Supplier Quality Management
Providing quality leadership at your supplier site. Quality assurance program development, implementation, and management across your supplier's production activities.
Supplier Monitoring
On the ground, process level supplier monitoring to track production progress, preemptively identifying risks, obtaining deep production insights, and real-time problem solving.
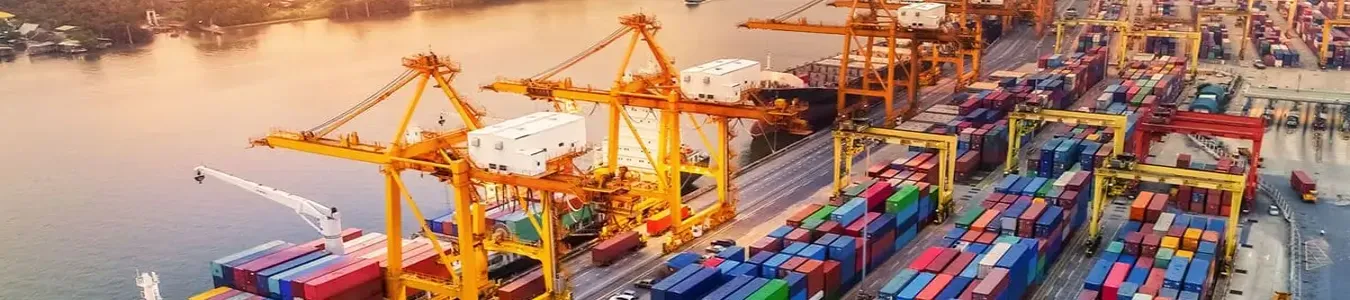
Your product quality is why your customers buy your products. It's the first thing that people say when they hold a product in their hands - 'wow, that product has great quality, that company is fantastic'. AMREP is the go-to company for putting your business in that position. We utilize a proactive quality control and problem-solving approach so that you don't find yourself chasing quality issues or with unsatisfactory shipments at your door. By this time, it's already too late.
Even if your costs of receiving defective products aren't high, or even if your supplier's quality performance is very high, having on-site supplier quality control gives you the assurance that there is somebody with your business interests in mind who's checking on your products and maintaining your quality expectations. There's also somebody who can solve quality issues even before they arise - this is far more effective and efficient than following-up on quality issues after you've received your product shipments
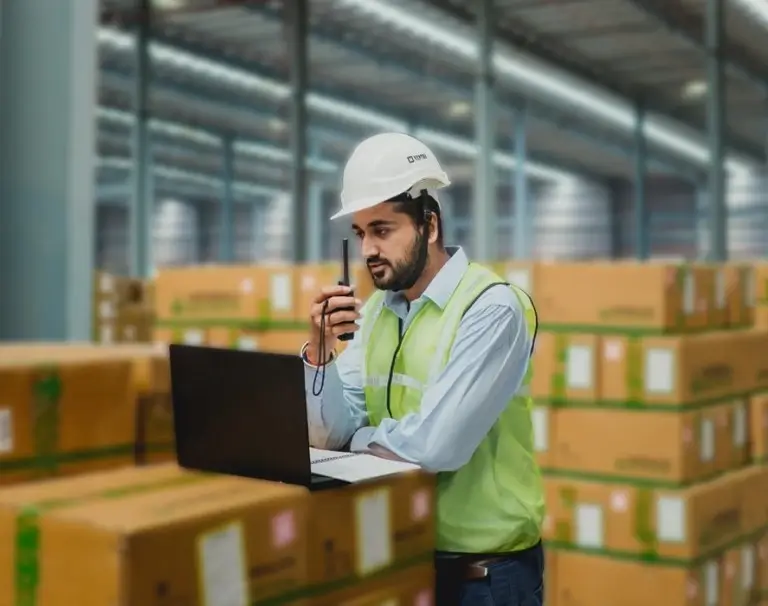
Whether it be small batch productions or high volume manufacturing situations, a multi-national contract manufacturer or small factory facility, we have the expertise to address all your quality and supplier quality management needs. Our staff are experienced quality engineering professionals with extensive hands-on manufacturing backgrounds.
- QMS development, assessment, and implementation
- Process control
- Quality remediation actions and problem solving
- Supplier corrective actions follow up and closures
- Quality performance improvements
- Driving supplier conformance to your quality requirements.
AMREP collaborates with a diverse range of partners across various industries:
- Automotive, new mobility, alternative transportation
- Aerospace and space
- Electronics, consumer technology,
- Robotics
- Medical devices
- Health and fitness technology
- Consumer products
- Industrial products
- Communication
- Adaptive technology
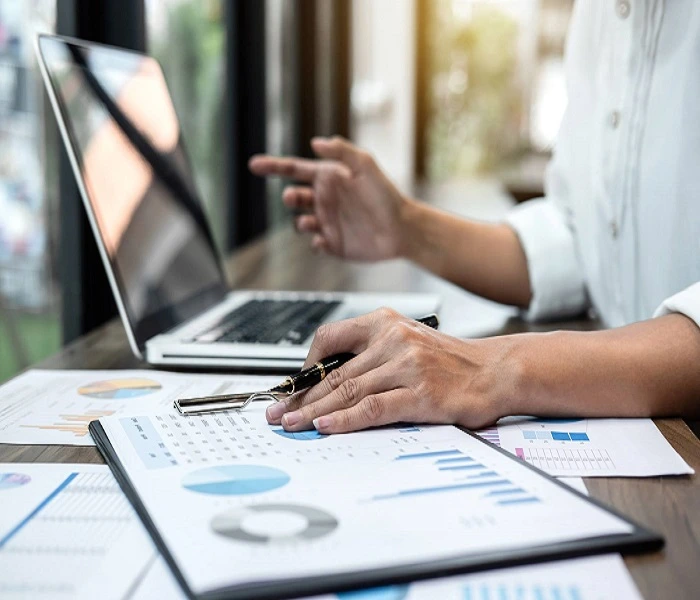
Kathleen Morgan, Engineering Director
Electronics/ consumer techOur company makes cutting edge robotic solutions for aged care. We’re a small company who needed to focus our resources on developing our engineering team; it would have been really expensive for us to develop our own in-house quality and manufacturing team. We found that AMREP was an excellent way of outsourcing our QA/QC function at an affordable cost - we obtained the expertise we needed, and we had AMREP engineers who could work directly with our vendors to implement our manufacturing requirements.
Hayley Williams, Director of Manufacturing
Consumer ProductsAMREP is our pre-shipment inspections partner at our sourcing locations in Asia and Mexico. We’ve been with them for more than 10 years. We like that their quality engineers and operations managers train the inspector teams themselves and take the time to properly study our products so that they apply the right inspection techniques.
Charles Bateman, Director of Operations
Health TechChoosing AMREP’s supplier management solutions was a brilliant move for our business. By having an AMREP SQE at our contract manufacturer site in Mexico, we saved considerable amounts of time and money in having to send our own team over although we’re based in the US. One major advantage was having somebody onsite who could follow up on the CAPA items we requested of the supplier.
Henry Jackson Lee, Director of Supply Chain
Medical devicesWe use AMREP Supplier Management Services to do source inspections and sustaining quality engineering activities at our final assembly site in China. Being in the medical devices industries, we are naturally extremely concerned about quality escapes in our supply chain. AMREP’s inspectors and quality engineers helped us to foster a quality management discipline at our supplier and reduce production issues.
AMREP Supplier Management Services gives you the tools you need to achieve effective quality control at your production or supplier site and assure your product quality. Our work approach is to proactively capture, resolve, and prevent quality issues at the source. Take advantage of our effective supplier quality control services to maintain competitive advantage, cost reduction, and business growth while minimizing quality issues in goods and services.
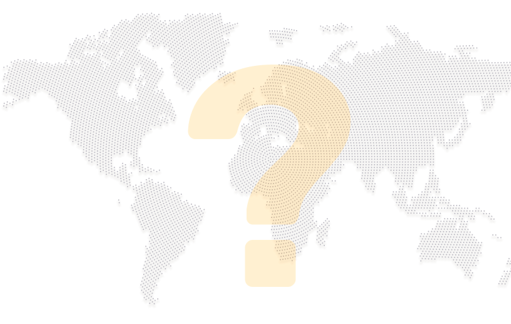
In the production and supply chain context, Quality Management Systems (QMS) is where companies establish a system for achieving quality in the materials, components, manufacturing processes, and final products they use and create. It consists of processes, processes, and technical parameters. Having a QMS helps to ensure that suppliers are providing their services or products of the highest quality according to your pre-established requirements.
ISO 9001: Provides a framework for global best practices in quality management.
IATF 16949: Tailored for the automotive industry to prevent defects and reduce waste.
AS9100: Meets the stringent requirements of the aerospace industry.
Six Sigma: Reduces process variation to improve quality.
Total Quality Management (TQM): A comprehensive effort to enhance customer satisfaction across all organizational operations.
It's not a bad idea to have third party supplier quality management even if you don’t have quality problems with your supplier. In our very volatile world, anything can happen and your supplier situation can change very quickly. They may experience production problems that will affect your next shipment, they may make an error because the suppliers staff, especially production line workers, change all the time. By having a third party supplier quality management company, you at least have boots on the ground who can check on the supplier and keep an eye on what's going on, and just see if everything is on track for you.
They don’t have to be there all the time. Supplier quality management companies have flexible price options and will be able to tailor something according to your work requirements and budget.
A third party quality control company or quality assurance provider will help you with effectively meeting your product quality, supplier performance, and quality assurance system objectives. You can achieve greater customer satisfaction with the quality of your products and minimize the risk of customer complaints or product recalls. Some clients also use third party quality control companies so that they can demonstrate compliance with regulatory or customer quality requirements. Quality control companies are your tools for solving and containing quality problems at the supplier source before it escalates through your supply chain and becomes more complex and costly to remedy.
Do you want to build a strong reputation for your organization? Are you looking for the best quality optimization techniques? No need to go anywhere! You have already found the third party supplier quality management services for all your needs. AMREP offers quality assurance services that deliver beautiful product quality and great supplier quality outcomes. Our staff is experienced quality professionals who come from manufacturing, engineering, and quality management backgrounds.
The role of a quality control inspector is to ensure that products meet the required quality standards and specifications. They inspect products at various stages of production to identify defects, deviations from specifications, and other quality issues. Quality control inspectors use various tools and techniques to conduct inspections, such as visual inspection, measurements, and testing. Their goal is to prevent defective products from reaching customers and to maintain consistent product quality.
Having a Quality Management System (QMS) is important because:
-
It provides a systematic approach for process improvement.
-
It will help you to identify quality issues, eliminate unnecessary activities, and close gaps in performance.
-
A QMS can reduce international and local regulatory risks in your organization as it enables you to meet quality requirements and standards.
-
It also has a transformative impact on your company culture, business outcomes, reputation, and customer satisfaction.
Third-party quality assurance services benefit multiple stakeholders by enhancing product quality and compliance, reducing manufacturing costs, and ensuring consumer safety. Manufacturers improve their production standards, while consumers enjoy reliable products. Retailers see fewer returns, protecting their brand reputation, and regulatory bodies can enforce safety standards effectively. Additionally, these services provide an external validation for a company's internal quality team, enhancing their capabilities and ensuring unbiased assessments.
Take a look at some benefits:
-
An agile approach to quality management
-
Flexible, connected adaptive solutions
-
Risk reduction in probable product failure
-
Improved product quality
-
Drive continuous business growth
-
Deliver exceptional customer experience
-
Effective control on quality to fill the performance gap
-
Effective compliance
-
Consistency: prevent delays and disruptions while staying on time and under budget.
-
Complete visibility between your production process, product record, requirements, issues, and related processes
Contact us today to start implementing a quality assurance framework that enhances your manufacturing processes.
Call Us
(00) 112 365 489
Mon - Sat 9.00 - 18.00
Sunday Closed
