We offer a range of inspection services tailored to meet your specific needs:
Our Services Include:
Pre-Production Inspection (PPI)
PPI ensures that your supplier's manufacturing process and materials align with your product specifications before production begins.
During Production Inspection (DPI)
DPI monitors production processes in real-time to identify potential defects early on.
Pre-Shipment Inspection (PSI)
PSI is the final step before shipment to ensure that the goods meet your agreed specifications, reducing the chances of costly returns and disputes.
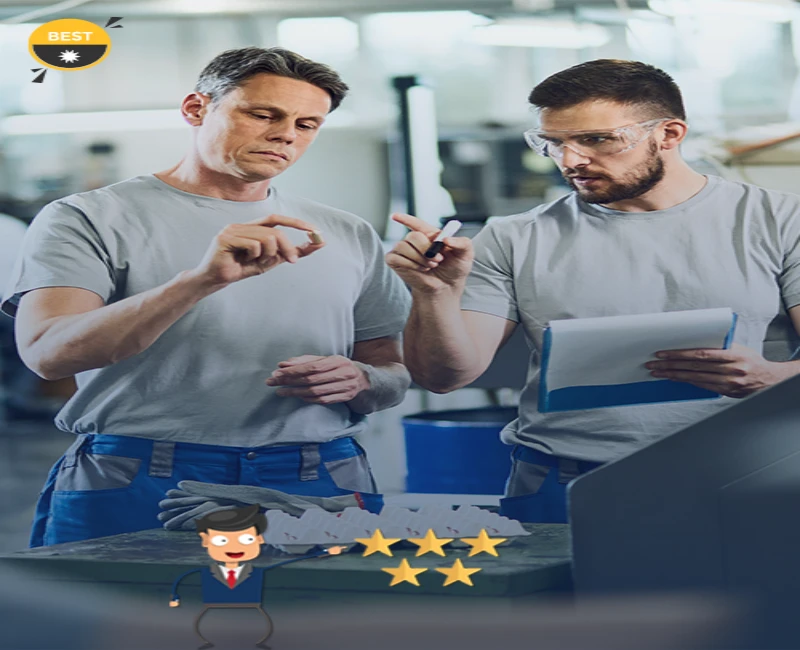
Thailand is a dynamic hub for manufacturing and production, but with a growing number of suppliers, the challenge to maintain consistent product quality increases. Our Quality Inspection Services offer the expertise and reliability you need. Here's why clients trust us with their quality control:
- Experienced Professionals Our skilled inspectors have expertise in international quality standards and various industries, including textiles, electronics, automotive, and consumer goods.
- Customized Reporting We provide clear, detailed reports with photos and notes, highlighting defects and suggesting solutions, tailored to your needs.
- Fast and Reliable Results Our efficient inspection process delivers timely, actionable results without compromising accuracy.
- Global Standards Compliance We ensure compliance with international standards like ISO 9001, AQL, and industry-specific regulations such as CE, RoHS, and FDA.
- Cost Efficiency We help reduce costs by identifying defects early, preventing costly recalls and returns, and enhancing your profitability.
Our team is equipped to handle inspections across a wide range of industries, ensuring quality across various types of products. Some of the sectors we serve include:
- Automotive
- Aerospace
- Electronics
- Medical and Health
- Solar and Photovoltaics
- Automation and Digital transformation
Consultation & Requirement Assessment:
We assess your needs, product details, and quality expectations to tailor the inspection process to your business goals.
Inspection Scheduling:
We align inspections with your production timeline, ensuring smooth coordination with suppliers.
On-Site Inspection:
Our inspectors perform thorough checks to ensure your product meets specifications.
Reporting & Recommendations:
We provide a detailed report with findings and corrective action suggestions.
Follow-Up:
We conduct re-inspections if needed to ensure all issues are resolved and quality is met.
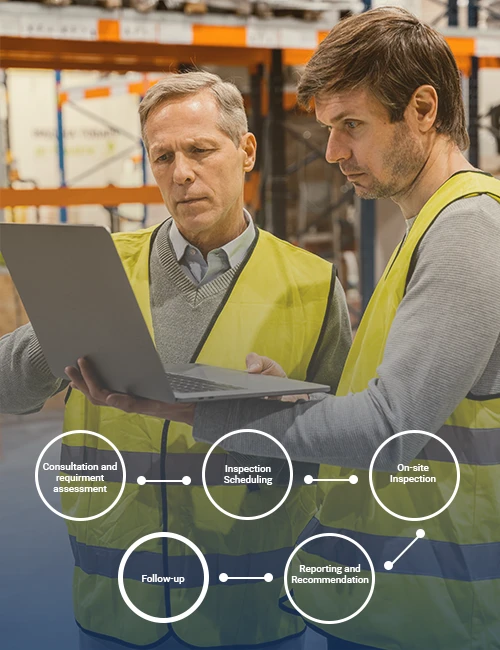
AMREP offers quality inspection services across Thailand, in key manufacturing hubs, providing efficient, tailored inspection solutions to meet your needs.
Our Thailand Locations Include:
- Bangkok
- Chonburi
- Rayong
- Samut Prakan
- Chiang Mai
Our clients across automotive, aerospace, electronics, medical devices, and more, consistently report improved quality control and reduced defects, highlighting our role in their continued success.
Kathleen Morgan, Engineering Director
Electronics/ consumer techOur company makes cutting edge robotic solutions for aged care. We’re a small company who needed to focus our resources on developing our engineering team; it would have been really expensive for us to develop our own in-house quality and manufacturing team. We found that AMREP was an excellent way of outsourcing our QA/QC function at an affordable cost - we obtained the expertise we needed, and we had AMREP engineers who could work directly with our vendors to implement our manufacturing requirements.
Hayley Williams, Director of Manufacturing
Consumer ProductsAMREP is our pre-shipment inspections partner at our sourcing locations in Asia and Mexico. We’ve been with them for more than 10 years. We like that their quality engineers and operations managers train the inspector teams themselves and take the time to properly study our products so that they apply the right inspection techniques.
Charles Bateman, Director of Operations
Health TechChoosing AMREP’s supplier management solutions was a brilliant move for our business. By having an AMREP SQE at our contract manufacturer site in Mexico, we saved considerable amounts of time and money in having to send our own team over although we’re based in the US. One major advantage was having somebody onsite who could follow up on the CAPA items we requested of the supplier.
Henry Jackson Lee, Director of Supply Chain
Medical devicesWe use AMREP Supplier Management Services to do source inspections and sustaining quality engineering activities at our final assembly site in China. Being in the medical devices industries, we are naturally extremely concerned about quality escapes in our supply chain. AMREP’s inspectors and quality engineers helped us to foster a quality management discipline at our supplier and reduce production issues.
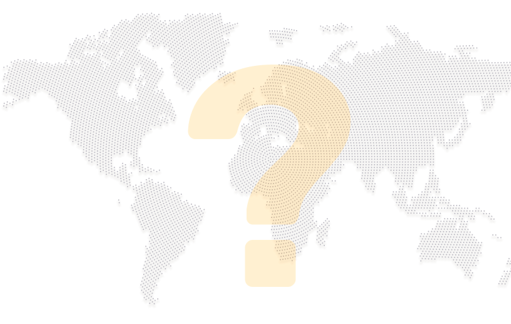
Yes, all of our quality inspectors are highly trained and certified according to industry standards. We ensure they are updated with the latest inspection techniques and compliance requirements.
After the inspection, you will receive a detailed report outlining the findings, including any areas of concern or recommendations for improvement. This report helps guide your next steps in production or quality assurance.
For an efficient inspection, ensure that the area, products, or systems to be inspected are accessible and ready. If you have specific concerns or questions, it's helpful to share those in advance with our team.
Yes, we can conduct inspections at various stages of production, from pre-production to in-process and final inspections. This helps to identify issues early on and ensure consistent quality.
If a defect is found, our inspectors will provide a detailed report, including the issue and potential solutions. We can also offer recommendations for corrective actions or help guide you through the process of resolving the issue.
No, we handle both small and large-scale inspections. Whether you're a small business or a large manufacturer, we can tailor our services to meet your specific requirements.
Yes, we offer customized inspection services based on your specific needs, including highly specialized tests and assessments for unique products or industries. Contact us to discuss your requirements.
All our inspectors are thoroughly trained and certified according to industry standards. They undergo continuous professional development to stay updated with the latest regulations, guidelines, and inspection techniques.
Typically, you will receive the inspection results within 24-48 hours after the inspection is completed. For more detailed or complex assessments, additional time may be required.
Yes, we offer expedited inspection services for urgent needs. Please reach out to us directly to discuss your timeline, and we will do our best to accommodate your request.
Yes, we provide inspection services globally. Whether you need an inspection locally or abroad, we can arrange for an inspector to visit your facility or site, wherever it may be.
Leverage agile framewokrs to provide a robust synopsis for strategy collaborative thinking to further the overall value proposition.
Call Us
(00) 112 365 489
Mon - Sat 9.00 - 18.00
Sunday Closed
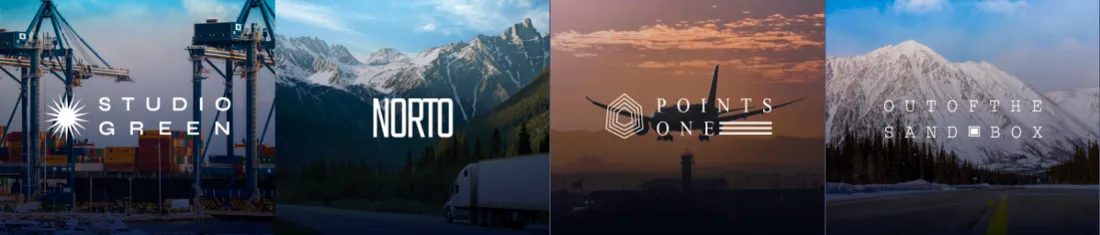